Introduction
The concept of refrigeration is very vital for the marine industry. Since early times ships are doing long voyages with sometimes a month of sailing. The provisions which are taken for such long voyages are perishable. Hence it is vitally important to preserve them.
Similar to household refrigerators ships have refrigeration rooms to store the food.Hence understanding the basics of refrigeration is highly vital for all the marine engineers.
Vapour Compression Cycle
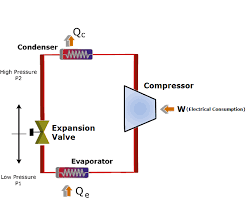
The marine refrigeration plant is based on the vapour compression cycle. The vapour compression cycle consists of the following important stages
- Compression- The refrigerant enters the compressor as a gas under low pressure and having a low temperature. The compressor does the work of pumping the liquid throughout the system. The refrigerant is compressed adiabatically and the refrigerant leaves the compressor having high temperature and high pressure.
- Condensation- The second important stage is condensation in this the refrigerant enters the condenser and releases heat energy to the cooling fluid. Refrigerants undergo a phase change but the pressure remains unaffected.
- Expansion- The refrigerant enters the expansion valve and it gets converted to low-pressure low-temperature liquid. Part of the refrigerant flashes off cooling the remaining refrigerant.
- Evaporation- The low-pressure low-temperature liquid then enters the evaporator. The heat from the surroundings is transferred to the refrigerant. It now gets converted to low-pressure high-temperature gas and goes to the compressor suction and the cycle repeats.
Types of Refrigerant
There are 2 types of refrigerants:
- Primary refrigerant- They are those refrigerants which take out heat from the space and undergo compression and expansion in the cycle.e.g.- R11, R12, R134a, R404 etc.
- Secondary refrigerant- They are those refrigerants which take out heat from the space and transfer this heat to another refrigerant which undergoes phase changes in a cycle. e.g.- brine, air.
Properties of a Refrigerant
- Properties of a Refrigerant
- Low Boiling Point- Refrigerant vaporizes in the evaporator to cool the surrounding. A lower boiling point means the refrigerant can turn easily into gas on absorbing heat. If refrigerant has a high boiling point then the compressor will have to work to create too much vacuum to lower the boiling point.
- Refrigerant should be easily condensable- This determines what pressure the compressor has to develop to condense the liquid in the condenser. Easily condensable gases will need a compressor to develop less pressure. This will reduce the size of the system
- High specific enthalpy of vaporization- Every kilogram of refrigerant should take out the maximum amount of heat thus increasing the efficiency of the system. Else more refrigerant will be required.
- High critical temperature- Critical temperature is the temperature above which the refrigerant cannot be liquefied at any pressure. It should be as high as possible. The sea water temperature is high near the equator and it will be impossible to liquefy the vapour refrigerant
- Low Specific volume-The gaseous refrigerant should occupy a small volume. Otherwise, it will occupy more space leading to bulkier systems.
- Non-corrosive
- Stable
- Non-corrosive and non-explosive.
- Miscible with lube oil
Marine Refrigeration Cycle:
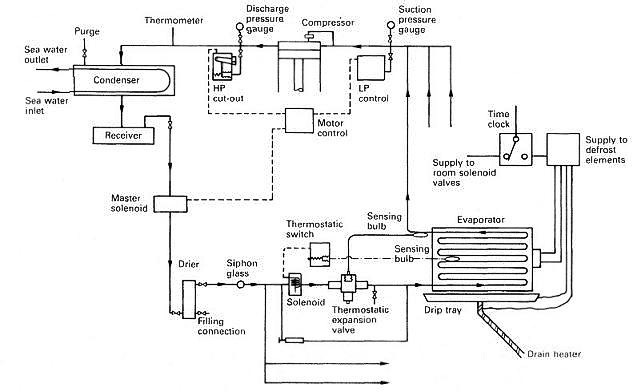
As seen from the figure, we can see the various components in the refer system. Instead of explaining how the system works which almost everyone knows I am going to go through a few important points which at times go missed.
- How the temperature of the room is maintained?
As seen in the figure, when the temperature of the room attains the set temperature, then the sensing bulb senses the temperature. This is given to the thermostatic switch. The thermostatic switch will convert this pressure signal into an electric signal and then gives it to the solenoid. This will cause the solenoid to shut. Due to this,there is no flow of gas and the thus the compressor cuts out on low pressure. When the temperature of the room rises above the set temperature a signal by the thermostatic switch opens the solenoid and as refrigerant starts flowing the compressor cuts in.
- What is subcooling?
Cooling of the refrigerant below its normal condensation point is known as subcooling. It can also be referred to under cooling. For example when water is cooled below 100 degrees Celsius, then it gets converted liquid state. If it is cooled to 96 degrees, then we say it is subcooled to 4 degrees. In a normal refrigeration system, a subcooling of 5-6 degrees is enough.
It is very important that the refrigerant is subcooled. This is because part of the refrigerant gets flashed off in the expansion valve and cools the remaining refrigerant. Higher the degree of subcooling lower is the amount of refrigerant that flashes off. We want less amount refrigerant to flash off so that more heat can be taken out from the cooled space
- What is superheat?
Heating of a refrigerant above its boiling temperature. For example, water boils at 100 degrees Celsius. If water is heated to 104 degrees, then it can be said as 4 degrees superheated. In a normal refrigeration system, a superheat of 4-5 degrees is enough.
We need the refrigerant to be superheated, as the degree of superheat will determine the phase of the refrigerant at the suction of the compressor. We want the refrigerant to be in the gaseous phase or else it can damage the compressor. Superheating of the refrigerant takes place in the evaporator.
- What are the safeties provided in the refrigeration compressor?
- Belt drive is given so that in case of hydraulic locking the belt would slip protecting the compressor
- Low pressure cut out.
- High-pressure trip
- Differential pressure trip
- Unloader to reduce starting torque
- The crankcase heater is provided.
- Suction is through the crankcase. Any refrigerant in the liquid form will be converted into gas due to high temperature of the refrigerant.
- Relief valve is given.
- Why back pressure valve is given for vegetable room?
Normally the temperature of bedrooms maintained at 4 degrees on the other hand meet room and fish room are maintained at – 14 and -12 degree Celsius respectively. Thus the refrigerant leaving the evaporator of the fish room and meat room will have higher pressure than that leaving the veg room. To prevent backflow of this refrigerant into the evaporator of the veg room a back pressure valve is given, since the outlet is common it is provided after the evaporator of the vegetable room.
Let’s discuss more in comments down below